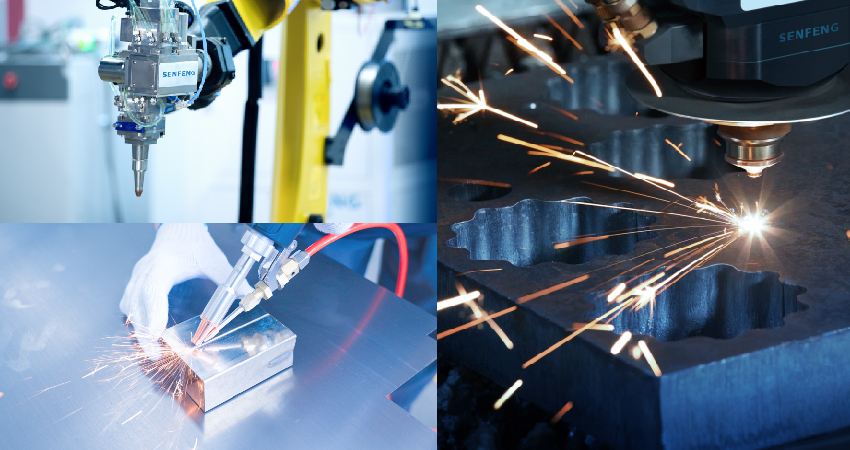
What Laser Technology Bring to the Bathroom Industry
Introduction
In the competitive world of bathroom manufacturing, efficiency and precision are paramount. A leading bathroom fixtures company in Uzbekistan recently made a significant leap in their production capabilities by investing in cutting-edge laser technology. This case study explores their acquisition of two handheld laser welding machines, one robotic laser welding machine, and a fiber laser cutting machine, highlighting the impact of these advancements on their operations.
The Challenge
The client operates in the bathroom fixtures industry, primarily manufacturing cabinets, showerheads, bathtubs, and various other plumbing components. With the Uzbek market experiencing rapid growth and rising consumer demand for high-quality bathroom products, the company faced significant challenges in their production processes.
Traditionally, they relied on outdated welding and cutting techniques, which included manual welding machines and basic plasma cutters. These methods resulted in longer production times and inconsistent product quality, leading to customer dissatisfaction. Specifically, the issues included:
- Precision: The manual welding processes often produced weak joints, making the fixtures less durable and prone to leaks.
- Efficiency: Slow cutting speeds and labor-intensive processes hindered their ability to scale production in response to market demands.
- Quality Control: Variability in product dimensions and finishes affected the overall aesthetic appeal of their bathroom fixtures.
To remain competitive and meet growing customer expectations, the company recognized the urgent need for advanced machinery. They sought solutions such as fiber laser welders and fiber laser cutters to enhance operational efficiency, improve precision, and ultimately elevate product quality.
The Solution
To address these production challenges, the client turned to SENFENG for a comprehensive solution. After closely analyzing their manufacturing processes, SENFENG developed an automated system tailored to their needs. This solution includes two 1500HWM handheld laser welding machines, one 1500CRW robotic welding machine, and a fiber laser cutting machine.
Handheld Laser Welding Machines
- Efficiency: Compared to traditional welding, laser welding machines offer faster welding speeds, especially for complex tasks.
- Aesthetic Welds: The precision of laser welding ensures clean, attractive weld seams. This is especially important in the bathroom fixtures industry, where appearance and quality are paramount.
- User-Friendly Operation: The intuitive design of handheld laser welders makes them easy to operate. Minimal training is required, enabling operators to quickly become proficient, thus reducing downtime and enhancing productivity.
- Low Pollution: Handheld laser welding produces minimal smoke and fumes compared to conventional welding processes. This results in a cleaner working environment, promoting safety and reducing the need for extensive ventilation systems.
- Flexibility: The handheld design allows operators to maneuver easily, making it suitable for both large and small components. The client also customized external equipment such as a rotating table and a wire feeder to meet various welding requirements
Robotic Welding Machine
- Automation: This machine automates the welding process, ensuring consistent quality across all products.
- Precision: With advanced programming capabilities, the robotic welder can execute intricate designs, enhancing the overall aesthetic appeal of the fixtures.
Fiber Laser Cutting Machine
- High Precision: This machine provides exceptional cutting accuracy, allowing for intricate designs that were previously challenging to achieve.
- Material Versatility: Capable of cutting through various materials, including carbon steel, stainless steel, aluminum, copper, it opens up new design possibilities for the company.
Implementation
The implementation process was seamless, thanks to the comprehensive training provided by the equipment suppliers. Operators quickly adapted to the new machines, and the learning curve was minimal. Within weeks, the company was fully operational with their new laser systems.
Results
The impact of the new technology was immediate and substantial:
Increased Production Efficiency
The company reported a 40% increase in production speed, allowing them to fulfill larger orders without compromising quality.
Enhanced Product Quality
The precision offered by the laser machines resulted in fewer defects and higher-quality finishes, leading to increased customer satisfaction.
Cost Saving
The reduction in production time and material waste translated into significant cost savings, improving the company’s overall profitability.
Market Competitiveness
With the ability to produce high-quality products more quickly, the company strengthened its position in the market, attracting new customers and retaining existing ones.
Customer Feedback
“This was our first time purchasing laser welding and cutting equipment,” Mark, the production manager, explained. “We made a significant investment in this upgrade, but from a long-term perspective, this equipment will allow us to produce higher-quality bathroom fixtures, something our customers are eager for. So far, we’ve seen a noticeable increase in production efficiency. The machines are able to handle more precise components, especially tasks that were challenging with traditional methods.”
Mark further emphasized the importance of training and support: “After the equipment was shipped, SENFENG sent engineers to help with installation, and we had two weeks of on-site training. This, combined with the training we received at their factory before delivery, was incredibly valuable for our team. It’s reassuring to know we have the support needed for such an advanced automation system.”
Conclusion
The strategic investment in laser welding and cutting technology has not only resolved the challenges faced by this Uzbek bathroom fixtures company but has also set a new standard for excellence in their industry. By embracing innovation, they have enhanced their production capabilities and positioned themselves for future growth. This case serves as an inspiring example for other manufacturers looking to modernize their operations and meet the evolving demands of the market.