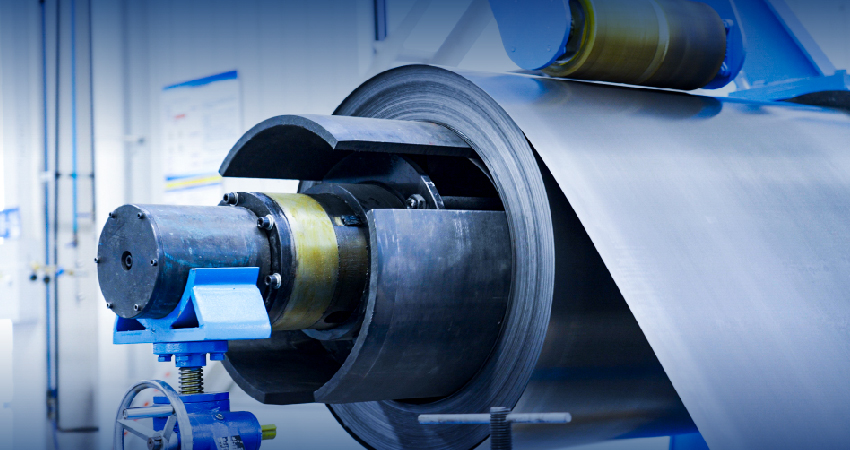
Driving Success in Battery Enclosures: The TOP Series
Client Background
Our client, a leading manufacturer in the UAE, specializes in producing essential components in the clean energy and EV industries, like energy storage, electric vehicles (EVs), and power control systems. With the growing demand for sustainable energy solutions in the Middle East, their business has expanded rapidly, necessitating an upgrade in their production capabilities. To keep up with the increasing orders while maintaining high-quality standards, the client needed a comprehensive solution to optimize their manufacturing process for energy storage battery enclosures.
Challenges Faced
Before contacting us, the client was facing several challenges:
Inefficient Production Workflow
Their existing production process lacked automation, which slowed down their output and created bottlenecks, especially during the bending and welding phases.
Inconsistent Product Quality
Due to manual interventions in several production steps, the accuracy and consistency of the enclosures varied, affecting the overall quality and increasing rework.
High Labor Costs
The heavy reliance on manual labor for tasks such as cutting, bending, and welding led to higher operational costs and variability in production speed.
Scalability Concerns
As demand grew, the client struggled to increase output without significantly increasing costs or compromising quality.
The Solution: Four TOP Series Automated Metal Processing Lines
After a thorough analysis of the client’s needs and production workflow, we recommended the installation of four TOP production lines. The TOP series is a complete flexible production line that includes a coil-fed laser cutting system, a panel bending machine, and a laser welding machine, enabling automated production from metal sheet uncoiling, cutting, bending, to welding.
A Decoiler
Automatically feeds metal sheets into the line, eliminating manual handling.
A Leveling Machine
Ensures perfectly flat metal sheets before processing, critical for maintaining precision.
A CNC Fiber Laser Cutting Machine
Performs high-speed, accurate cuts tailored to the specifications of the enclosures.
Three Robots
Two feeding robots automatically transport cut workpieces to the bending unit, then move the bent parts to the welding station, where a welding robot completes the final process. This minimizes manual handling and greatly improves efficiency.
A Panel Bender
Accurately shapes the metal sheets into the required form for the enclosures, ensuring consistent results with minimal waste.
A Laser Welding Machine
Delivers precision welding to complete the enclosure assembly, ensuring durability and strength in the final product.
These machines are fully integrated with each other, creating a seamless, end-to-end solution that optimized the entire manufacturing process. The client’s facility was transformed into a smart factory, utilizing advanced automation to address their production challenges.
Customer Feedback-Why SENFENG
“Our decision to buy these four automated TOP production lines was mainly to manufacture energy storage battery enclosures,” explained Mark, the Purchasing Manager. “We’d been planning this purchase since early last year. We went with Senfeng for a few key reasons. First, they specialize in metal forming equipment and produce the entire TOP series in-house, which gave us confidence in the quality and delivery time. Second, they’ve sold a lot of machines—cutting, bending, and welding—in the UAE, so they’ve got a strong brand here, and their pricing is pretty fair. Plus, their solid experience with equipment maintenance was a big plus for us.
Learning to operate automated equipment was definitely a challenge. During the production phase, we sent our engineering team to Senfeng’s factory in China for training. Once the machines arrived, Senfeng sent their team over to help with installation and gave us two weeks of training. Now that we’ve built up a lot of hands-on experience, the equipment is fully up and running.
Even though the upfront cost was high, we believe automated production is the future and will be a key part of our competitive edge.”
Results Achieved
The installation of the TOP production lines brought immediate and long-lasting improvements to the client’s production process:
Enhanced Efficiency
The customer mainly cuts thin metal sheets, which is where the fiber laser cutting machine excels, greatly improving cutting efficiency. Totally, automation reduced cycle times by up to 50%, allowing the client to meet rising demand without compromising quality.
Improved Product Quality
With precise cutting, bending, and welding operations, the consistency and durability of the energy storage enclosures improved dramatically.
Cost Savings
In the past, the customer had to hire a third party to level and cut the coil into sheets before processing. Now, with the TOP series, they can handle everything from coil to finished product in-house, significantly reducing production costs.
Scalability
With the new production lines in place, the client now has the capacity to easily scale their production as market demand continues to grow.
Conclusion
By automating key aspects of the production process, we helped our client in the UAE overcome their manufacturing challenges, allowing them to produce energy storage battery enclosures with greater efficiency, precision, and scalability. This not only strengthened their position in the market but also laid the foundation for future growth in the renewable energy sector.
For companies looking to optimize their production lines and stay competitive in the fast-evolving energy storage industry, our TOP production line offers a proven, reliable solution.