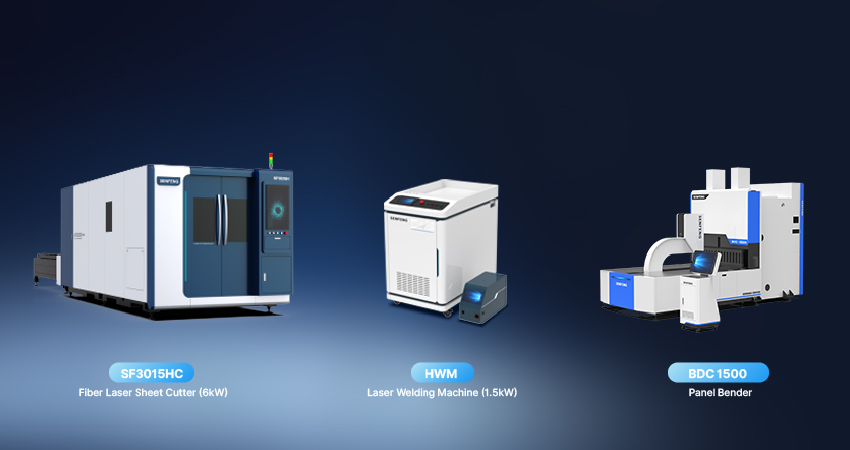
Streamlining Distribution Cabinet Manufacturing
Customer Background
Our client, established in 2018 and based in India, specializes in the production of distribution cabinets. With two existing factories and plans to expand by constructing a third, the company aims to enhance its production efficiency. They have built a strong reputation for delivering high-quality products tailored to meet the diverse needs of their customers. Their strategic vision emphasizes innovation and efficiency, driving the demand for advanced manufacturing technologies. To achieve their goals, the client is looking to invest in modern equipment that will not only improve operational efficiency but also uphold the high standards of quality they are known for.
Challenges Faced
The production process for distribution cabinets at our client’s facility involves several key steps: design, procurement of metal sheets, cutting, bending, welding, surface treatment, assembly, and quality inspection. They utilize 3 plasma cutting machines for the cutting phase, 2 press brakes for bending, and 4 manual arc welders for assembly. Despite their robust production capabilities, the client faces several challenges that impact efficiency and quality:
Lack of Precision
The existing production equipment lacks precision; for example, in the cutting phase, the results of plasma cutting for some critical components are not ideal, leading the client to outsource certain parts.
Inefficient Production
The automation level of the press brake and arc welding equipment is not very high, requiring skilled workers for operation, which is time-consuming and labor-intensive. This has made product delivery times a major headache for the client.
Material Waste
Traditional cutting techniques often resulted in significant material waste, impacting the overall cost-effectiveness of their operations.
Limited Flexibility
The lack of advanced machinery hindered the client’s ability to adapt to changes in the distribution cabinet market, such as increasing demands for customization and energy-efficient designs. This limitation affected their capacity to meet deadlines and deliver high-quality, tailored solutions.
High Labor Costs
The reliance on manual labor for cutting and fabrication increased operational costs, affecting profitability.
Solution
To address these challenges, the client decided to invest in advanced manufacturing equipment from a reputable supplier. They opted for:
SF3015H Fiber Laser Cutting Machine (6kW)
Compared to plasma cutting machines, the 6kW fiber laser offers higher cutting quality, which is reflected in its superior cutting precision, attractive edge finish, and smaller heat-affected zone. This reduces the workload for subsequent surface treatment of cabinets. The laser cutting machine excels in cutting commonly used materials for distribution cabinets, such as cold-rolled steel, carbon steel, stainless steel, and aluminum, particularly in the 1-4mm thickness range.
BDC1500 Panel Bender
Compared to a press brake, the bending machine offers a higher level of automation. It allows for automatic bending of workpieces by simply inputting the program, eliminating the need for manual adjustment of bending positions. This automation provides a significant competitive advantage in mass production, enhancing both quality and speed.
SF1500HWM Laser Welding Machine
With the introduction of the laser welder, workers can operate the equipment after minimal training. The resulting welds are aesthetically pleasing, significantly enhancing product consistency.
Negotiation Process
In June 2023, our client visited our facility in India and expressed satisfaction with the cutting samples, initially planning to purchase a 3kW CNC fiber laser cutter and a handheld laser welder. However, as it wasn’t the right time for procurement, they didn’t place an order. In April 2024, the client returned to our Dubai branch for another equipment inspection. After reassessing their production needs, they realized that a 6kW cutting machine would better suit their high production volume, alongside an additional panel bending machine for batch processing.
During this time, the client explored options from other manufacturers but ultimately chose SENFENG. “After careful consideration, we decided to partner with SENFENG,” said Sameer, the company’s supervisor. “We were pleased with the results of both factory visits. Additionally, SENFENG’s diverse product line meets our needs from cutting to bending and welding. Purchasing from the Dubai branch allowed us to avoid lead times, saving us significant time.”
Results
The implementation of the new equipment led to a remarkable transformation in the client’s production capabilities. Within a short period, they reported:
- A 30% reduction in production time, allowing them to meet tight deadlines and increase customer satisfaction.
- A 25% decrease in material waste, translating into substantial cost savings and improved sustainability practices.
- A 20% increase in production capacity, enabling the client to expand their market presence and take on new projects.
The successful integration of the SF3015H, BDC1500, and SF1500HWM has positioned the client for sustained growth and competitiveness in the distribution cabinet and switchgear market.
Conclusion
By investing in our fiber laser cutting machine, fiber laser welder, and panel bending center, the Indian client has successfully transformed their production processes into automated, high-efficiency batch operations. This significant shift not only streamlined their manufacturing but also greatly enhanced their competitive edge in the market. As they continue to leverage advanced technology, the client is well-positioned to meet increasing demand and drive further growth, showcasing the powerful benefits of modernizing production capabilities.
If your company is facing similar challenges, consider exploring innovative manufacturing solutions to elevate your production capabilities and drive growth in your industry.